The purpose of indoor agriculture is to provide plants with a protected and controlled environment allowing for year-round crop production, optimal growth, and maximum profits. Greenhouses are the best way to maintain a controlled environment yet also harness the (free) power of the sun. Even with the sun piping in its rays there is a need for supplemental lighting to enhance and speed up the vegetative cycle and assist during flowering in long-day plants. As LEDs have become more and more prominent, are widely recognized as the future of lighting and are proving their worth in regards to return on investment, this discussion is shaped around them.
As someone whose team has decades of experience in lighting, it is simply astonishing that there aren’t more discussions in the community around LEDs and light delivery. Looking back at HPS and CMH lights, the battle for who was “best” came down to efficiency and hood design. The best hoods or reflectors had the highest reflectivity ratings and spread out the light in the most even fashion over the canopy. This begs the question, why aren’t we having these same discussions with LEDs? It could be because LEDs have largely been used in vertical farming where hoods/optics are less of a concern. It is interesting, however, to see the lack of research and consumer demand around this topic especially as it relates to greenhouse applications. Greenhouses are inherently artificial lighting disadvantaged due to their high roof lines and need to minimize shadowing or blocking of the sun. For LEDs, this means a design that is completely backwards to what works in vertical farming.
Similar to how HPS and CMH lights utilize hoods to control the delivery of light, LEDs have optics at their disposal. Let’s take a minute and dive into the basics of optics for LEDs. A bare LED, along with most other types of lights used in horticulture, has light energy that is emitted in equal intensity in all directions. The problem with that is, as you get off angle, the light spreads out exponentially. Meaning that as you move further away from directly under the LED, the lower the energy on your plants gets. This is where optics come into play. Since LEDs can have primary and/or secondary optic we should learn a little about each of these.
The Primary Optic
The primary optic is a part of the LED itself, built-in by the manufacturer, and is usually a small dome that sits on top of the diode. Its purpose is to give a general shape to light being emitted, but hardly in a definitive way. Many of the newest and most efficient LEDs have no primary optics at all as efficiency is the key driver amongst today’s consumers.
In horticulture, if an LED doesn’t have a secondary optic, then it translates into PPFD on your plants being reduced as you move away from the center due to the fact that LEDs natively emit a majority of their relative intensity on the center axis. The emitted light will continue to decrease intensity as it moves further away from the center. This centric concentration has a tendency to burn plants and really doesn’t promote deep penetration into plant canopies.
Secondary Optic
Secondary optics are used to capture ALL the photons emitted from an LED and direct it, through the specific secondary optic, in a controlled way onto a surface. This allows the optic designer to change the shape of the beam of light and, for horticulture, remove the hot spots and spread the light out evenly. It also provides for a sharp cut-off so the light emitted doesn’t get wasted on walls or aisles.
While there are many companies designing optics, such as Ledil, Carclo, and Khatod. Scynce LED was one of the first to optimize optics for horticulture; both from the output pattern as well as the LED package selection. There is no lighting application in the world that demands the extreme power levels and efficiency as does indoor cannabis/hemp farming. This is why off the shelf optics designed for other industries, just didn’t work. It required a new way of thinking, a different angle of approach and some creative engineering.
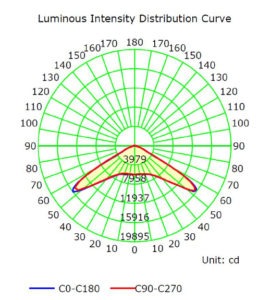
Scynce LED’s first horticulture specific optic was the Conic 120, launched in 2017. This optic was designed to have an equal output angle and intensity in all directions. Thousands of users have proven time and again that there is nothing that works better for vertical applications, where the light really needs to spread out quickly. The Luminous Intensity Distribution Curve, taken from a goniophotometer, shows that the red and blue axes (a good analogy here is that red is North to South and blue is East to West) are identical. When viewed from a top-down perspective, the curve would look circular, or like a traffic cone.
The Conic 120 optic is one of the key factors that make the Scynce’s “Raging” line of products such a success and a standout amongst a sea of sameness. There is a high quantity of LED’s, needed to spike the efficiency, coupled with enough of an angular pattern to allow plants to rage due to a unique concept called cross-beaming. Without secondary optics light is shared via splashing or cross-lighting. Cross-beaming is unique in that it has high intensity vectors of light penetrating the canopy at different angles to grow deep.
Greenhouse
After the Conic 120 optic was released and had a couple years of impressive results from the field, Scynce turned their focus to greenhouses. We tasked our in-house engineering team along with some of the best optical specialists in the world to develop a solution that had a different approach than the rest of the market was chasing. Thirty optical designs later, we finally had a breakthrough. Although today’s computer simulation software allowed us to iterate very quickly and build out a virtual model of each new optic that was developed, we didn’t want to design a light based on theoretical statistics only. In the end, the iterative process took almost three years because we spent the time to test each development over real plants.
The result was a new linear optic designed to (i) house up to 60 watts of LEDs under each optic and (ii) push the light out at 70 degrees in the long axis and 120 degrees in the short axis. This new optic, called the Linear 70, ticked all the boxes and solved most of the light delivery challenges when using LED’s in a greenhouse, or a high ceiling, indoor, single-level farm.
These two key features, LED density per optic and a dual-beam light delivery system, have multiple advantages over traditional optics or no optics at all.
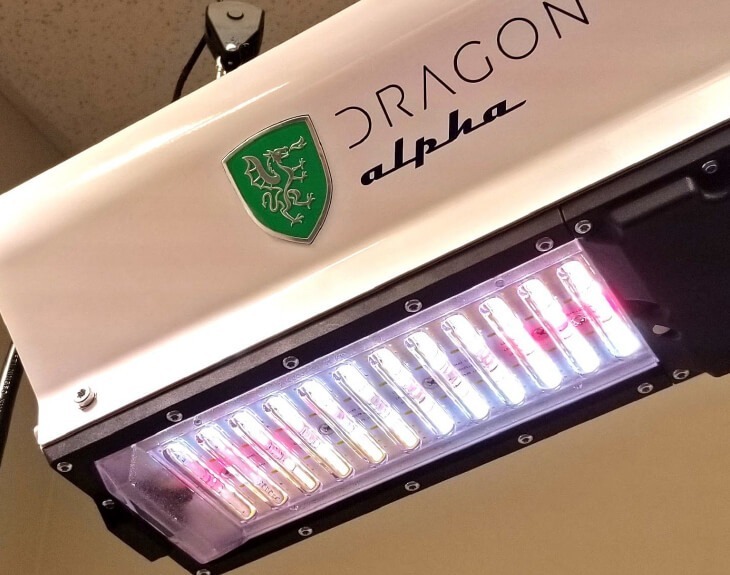
LED Density
Conventional optical design has a single LED under a single optic, or a large array of LED’s under a diffuser or reflecting chamber. Diffusers work great in general lighting (offices and schools) where 3 watts/sf is considered bright and smoothness is key. A single high power LED under a single optic is ideal for a flashlight, an automotive light or where plants are very close to the light fixture. High DLI plants, including cannabis, require light intensities in the range from 25-50 watts per square foot. To get that many LED’s under single optics requires a very large fixture. This is exactly what vertical farming requires, when light to canopy heights are sub 24”, but the last thing we want to do is block sunlight in a greenhouse. Employing the Linear 70 optical design, with up to twelve, five watt LED’s under a single optic, allows for a 22% increase in efficiency as compared to running a single LED per optic (in the same size housing and at the same power level). This brings total fixture efficiency within range of the equivalent single optic vertical farming light yet maintains the many benefits of using secondary optics to optimize light delivery while keeping a small fixture footprint.
Dual-Beam Light Delivery
The last thing anyone wants to do is block all of the bright beautiful sunlight that streams into greenhouses. With this in mind, a long and skinny light is ideal as it can be hung along the support beams, minimizing any shadowing. The Linear 70 optic was purposefully designed to take advantage of these end-to-end hanging requirements, which is why, in the long axis of the light, we have a nice tight 70 degree angle. In the other axis, the next beam or girder could be 10’ or more apart. In the effort to bridge that gap, the light output in the cross axis is a nice and wide 120 degrees. Once multiple lights are hung in a grid over the canopy, the dual beam technology blends together to produce an even PPFD while also penetrating deep.
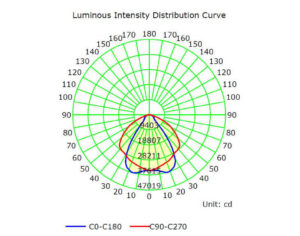
The diagram to the right shows the Intensity Distribution Curve for the Linear 70 optic. The blue line represents the long axis of the light while the red line represents the short axis.
A greenhouse with lights that are 5-10 feet over plants is the worst case for LED lights with no optics. All of that height and no optics means light will be spilled and wasted on walls and aisles. The intensity distribution curve shows that when using the Linear 70 optics, virtually all emitted light is delivered directly to the plants.
Lights are one of the most expensive yet important capital expenditures for indoor farming, with the cost of energy coming in as a close second. Light delivery is a topic that needs more discussion and exposure as it directly impacts a significant recurring cost to all cultivations. In today’s world we typically only talk about how much horsepower (total fixture efficiency) our cars have yet we neglect to talk about the tires (optics/reflectors) needed to direct that power (PPF) to the road (plant canopy) and measure its 0-60 time (PPFD). Horsepower doesn’t win car races and total light output and fixture efficiency ratings don’t grow plants.